Recycled plastic plays a critical role in advancing sustainable manufacturing by significantly reducing waste and generating valuable materials across multiple industries.
Maintaining the quality of recycled plastic is essential for ensuring safety, consistency, and customer satisfaction.
This article examines the definition of recycled plastic, emphasizes the importance of quality control in its production, and outlines the necessary measures to uphold high standards.
Additionally, it addresses how businesses can effectively implement these practices to improve their recycling initiatives and contribute to the overall recycling value chain.
Key Takeaways:
What is Recycled Plastic and its Role in the Recycling Process?
Recycled plastic refers to plastics that have been processed and repurposed from post-consumer waste, transforming materials such as polypropylene, polyethylene, BOPP, HDPE, nylon, and multi-layer film scraps into new, usable products.
This process not only aids in reducing plastic waste in landfills but also promotes environmental sustainability by decreasing the demand for virgin materials and minimizing the overall ecological footprint associated with plastic production.
Why is Quality Control Important in Recycled Plastic Production?
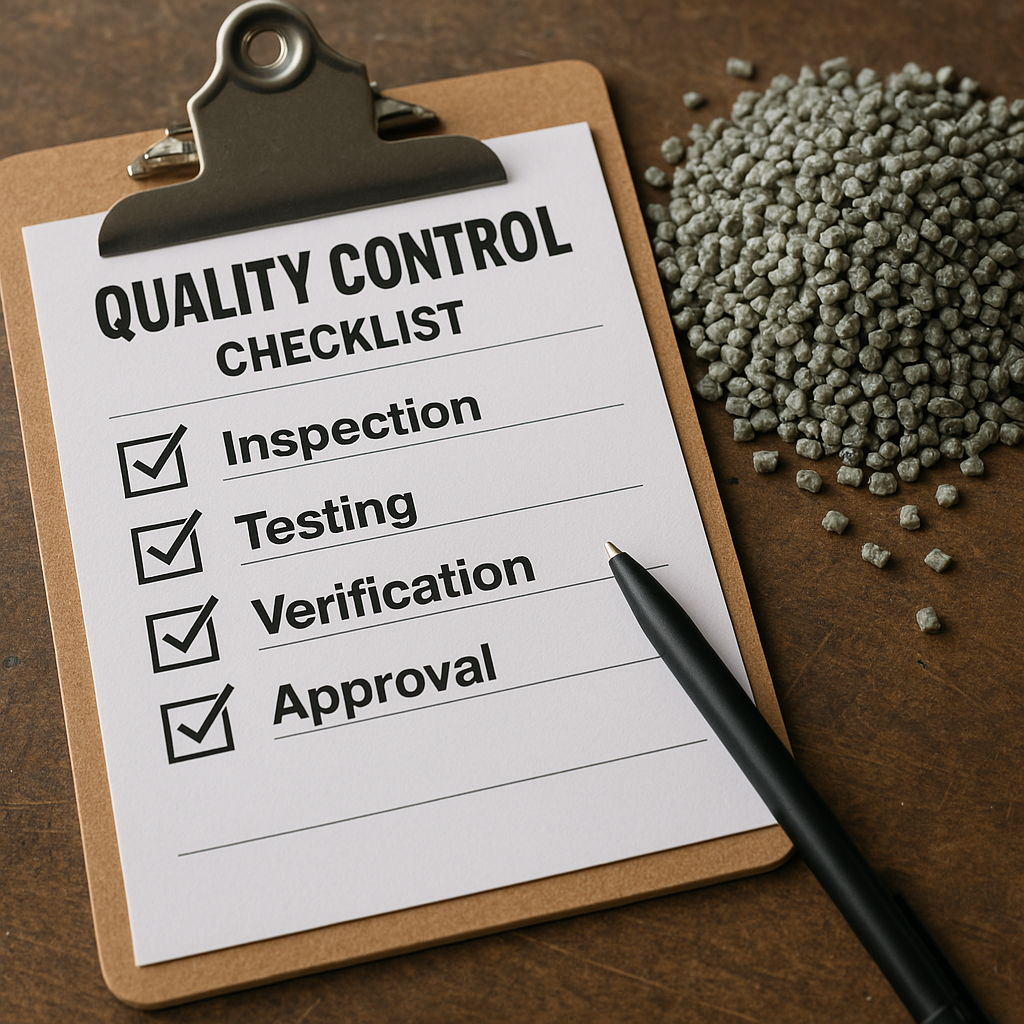
Quality control in the production of recycled plastic is crucial to ensure safety, adhere to compliance regulations, and uphold customer satisfaction, while addressing manufacturing challenges. It guarantees that the recycled materials produced are free from contaminants and meet the performance specifications required by brand owners.
By implementing rigorous testing protocols and conducting thorough product inspections, manufacturers not only ensure compliance with industry standards but also enhance the reputation of recycled products within the marketplace.
To Ensure Safety and Compliance
Ensuring safety and compliance in the production of recycled plastics is of utmost importance, as non-compliance with regulations can pose significant risks to both consumers and manufacturers, including potential health hazards associated with contaminated recycled materials. Regular quality assessments using techniques like X-ray fluorescence and infrared spectroscopy are essential.
The significance of adhering to compliance regulations cannot be overstated, as these regulations act as safeguards against the dangers that may arise from improper handling and processing of recycled materials. Without rigorous quality testing, the integrity of these materials can be compromised, potentially allowing harmful substances to enter the market.
Regular quality assessments are essential in confirming that recycled products meet established safety standards.
- Testing processes are instrumental in identifying contaminants that could jeopardize consumer health.
- Quality assurance practices not only enhance the reliability of recycled products but also foster trust among stakeholders.
- Ensuring compliance ultimately contributes to a more sustainable economy through the responsible use of resources.
By prioritizing safety and quality within the recycling industry, it is possible to unlock the full potential of recycled materials while safeguarding public health and the environment.
To Maintain Product Consistency
Maintaining product consistency is essential in the production of recycled plastic, as variability can lead to performance issues, customer dissatisfaction, and reduced production efficiency, impacting the recycling value chain.
Therefore, it is imperative to implement a robust quality control system that includes regular product inspections.To achieve the highest standards in production quality, several methodologies are employed. Statistical process control (SPC) plays a critical role in monitoring and regulating manufacturing processes, addressing performance characteristics and quality assurance.
By analyzing data collected at various stages, manufacturers can identify trends and anomalies that may disrupt the consistency of the final products.Regular inspections throughout the production cycle are vital to promptly address any deviations from established quality benchmarks. These inspections typically encompass:
- Sampling techniques to assess material properties
- Visual inspections to identify defects
- Testing for compliance with industry standards
Integrating these quality control systems not only enhances production efficiency but also fosters customer trust, as consistent quality is fundamental to ensuring customer satisfaction and loyalty.
To Meet Customer Expectations
Meeting customer expectations in recycled plastic production requires a thorough understanding of the performance demands associated with various applications. This understanding necessitates a commitment to quality assurance practices that ensure the end products meet the requirements of brand owners and their customers.
To achieve this alignment, manufacturers must undertake a comprehensive assessment of customer feedback and market trends, thereby establishing a dynamic framework that allows for necessary adjustments. By implementing robust quality control measures throughout the production process, companies can better address these performance demands. This includes:
- Investment in advanced testing technologies to assess material strength and durability.
- Regular training for staff on best practices and innovations in recycling processes.
- Adoption of a customer-centric approach, wherein the needs of end-users guide production priorities.
Through this methodology, manufacturers not only enhance customer satisfaction but also cultivate a reputation for reliability and excellence in recycled plastic products, thereby positioning themselves for long-term success in an increasingly competitive market, responding to evolving sustainability goals.
What are the Quality Control Measures in Recycled Plastic Production?
Quality control measures in the production of recycled plastics are essential for ensuring the integrity and safety of recycled materials. These measures encompass a comprehensive range of processes, including initial sorting and separation, as well as thorough testing for contaminants.
All of these processes are designed to maintain the highest standards within the production line.
Sorting and Separation
Sorting and separation are essential initial steps in the recycling process, during which advanced sorting technologies like color measurement and inspection criteria are utilized to effectively remove contaminants and ensure that only suitable materials are prepared for further processing.
These technologies include optical sorting systems, which employ cameras and lasers to identify materials based on their color and composition, as well as air classifiers, which separate materials according to weight and aerodynamic properties. Such sophisticated methods significantly enhance the efficiency of recycling facilities by improving output quality while minimizing the risk of contamination.
Additionally, magnetic separators and eddy current separators play a crucial role in the extraction of ferrous and non-ferrous metals, ensuring that valuable resources are not lost during the recycling process. By implementing cutting-edge sorting technologies, the recycling industry is advancing its mission to promote environmental sustainability and reduce landfill waste.
Cleaning and Shredding
Cleaning and shredding are essential processes in the production of recycled plastic, wherein effective cleaning procedures are implemented to eliminate dirt and residues. This is followed by shredding to prepare the cleaned materials for further processing and to regulate moisture content.
The initial cleaning phase is of utmost importance, as it ensures that contaminants such as oils, labels, and other foreign materials do not compromise the integrity of the recycled product. Techniques such as chemical washing, mechanical scrubbing, and rinsing using high-pressure water systems are employed to achieve optimal cleanliness.
Subsequently, the materials are subjected to precise shredding to facilitate uniform size reduction. This step is critical for enabling more effective drying and further processing, as inconsistent particle sizes can result in uneven moisture levels. Using a moisture analyzer, key practices during this process include:
- Monitoring moisture levels throughout the shredding process.
- Utilizing specialized shredders that incorporate moisture control features.
- Evaluating material quality through sampling post-processing.
By meticulously controlling moisture content, the quality of the final recycled material is significantly enhanced, leading to improved performance in subsequent applications.
Testing for Contaminants
Testing for contaminants in recycled plastics represents a critical quality control measure, involving specific testing protocols designed to identify and quantify impurities. This process ensures that the final product adheres to industry standards and meets customer specifications. Such a comprehensive approach to contamination assessment not only enhances the safety and performance of the materials utilized but also aligns with sustainability objectives, fulfilling environmental regulations and addressing consumer demands for safer, high-quality products.
Various testing methods are instrumental in detecting contaminants, enabling manufacturers to implement rigorous standards throughout the production process. Key testing protocols include:
- Infrared Spectroscopy: This method is employed to identify specific chemical bonds within materials, offering insights into the composition of recycled plastics.
- Gas Chromatography: Frequently utilized to detect volatile organic compounds (VOCs), this technique ensures that any potentially harmful substances are identified promptly within acceptable process parameters.
- Mass Spectrometry: This method is beneficial for quantifying the levels of various contaminants, ensuring they remain within acceptable limits.
These testing methods play a significant role in contamination control, facilitating compliance with regulatory frameworks and enhancing trust and quality assurance for end-users.
Melting and Filtering
The melting and filtering processes in recycled plastic production are critical stages that transform clean, shredded materials into uniform molten plastic. This molten plastic must subsequently be filtered to eliminate any remaining impurities, thereby ensuring optimal performance characteristics.
During these stages, specific techniques are essential in determining the quality of the final product. The melting phase employs controlled temperatures and consistent heating techniques to dissolve the plastic without degrading its inherent properties. This meticulous management not only influences the viscosity of the molten material but also impacts its capacity to be effectively shaped and molded.
Subsequently, the filtering process utilizes various filtration methods, such as screen or rotary filters, to remove contaminants that could compromise the integrity and durability of the recycled plastic. The integration of these techniques guarantees that the final product demonstrates enhanced mechanical properties and increased resistance to wear and tear, ultimately resulting in improved performance across diverse applications.
Pelletizing and Blending
Pelletizing and blending represent the final stages in the recycling process, during which molten plastic is transformed into recycled polyethylene (rPE) pellets and combined with other materials to produce a homogeneous product suitable for various applications, including agricultural products and industrial uses.
This phase is critical as it not only facilitates the processing of material into manageable shapes for handling but also addresses the necessity for consistent quality. The pelletizing process involves converting recycled plastics into small, uniform pellets through techniques such as extrusion or granulation, which optimizes flow characteristics during manufacturing.
Following the production of the pellets, blending becomes the focal point. This stage entails the careful integration of rPE pellets with additives or other plastics to enhance attributes such as strength, durability, or color. Effective blending ensures an even distribution of materials, which is essential in manufacturing end products that meet specific performance standards.
- Pelletizing: Converting recycled material into uniform pellets.
- Blending: Mixing pellets with additives for enhanced properties.
- Quality Control: Ensuring uniformity for reliable production outcomes.
How Can Businesses Implement Quality Control in Recycled Plastic Production?
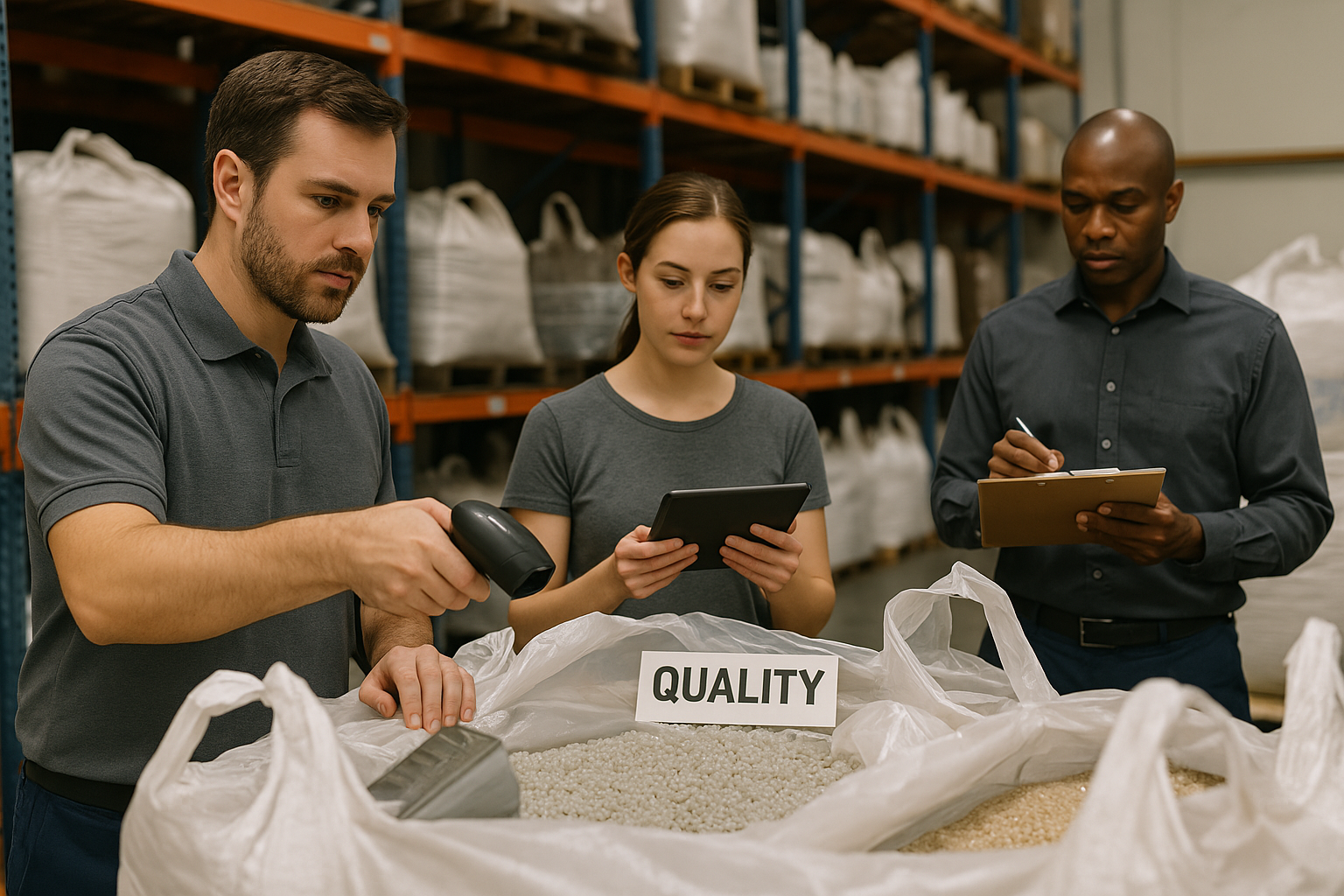
Implementing effective quality control in recycled plastic production necessitates that businesses establish standard operating procedures, invest in quality control equipment, provide employee training, and collaborate with certified recycling facilities.
These measures are essential for enhancing product quality and ensuring compliance with industry standards.
Establishing Standard Operating Procedures
Establishing standard operating procedures (SOPs) is essential for effective quality control in recycled plastic production. These documented processes provide clear guidelines for each stage of the recycling operation, ensuring consistency and compliance with established quality standards.
These procedures serve not merely as regulatory checklists; they actively promote best practices that enhance efficiency and foster trust in recycled materials. Without adherence to robust SOPs, the recycling process may experience inconsistencies that could compromise the quality of the final product.
By implementing a standardized framework, organizations can:
- Mitigate risks associated with contamination and improper processing
- Ensure that employees are well-trained and informed about the latest recycling techniques
- Facilitate regular assessments and updates, incorporating technological advancements
Ultimately, the rigorous application of SOPs contributes to maintaining and improving the overall integrity of the recycling operation, thereby resulting in increased consumer confidence and a sustainable future.
Investing in Quality Control Equipment
Investing in quality control equipment, such as moisture analyzers and capillary rheometers, is essential for recycling facilities. These tools facilitate the precise measurement and monitoring of critical parameters that significantly influence the quality of recycled materials.
Plus these fundamental instruments, various other types of quality control equipment play crucial roles in achieving optimal standards. For instance,
- Spectrophotometers are vital for analyzing the composition and purity of materials, ensuring that contaminants remain within acceptable limits.
- Particle Size Analyzers assist in understanding the distribution and size of particles, which is essential for determining material suitability for specific applications.
- Viscometers measure the viscosity of materials, providing insights into how they will behave under different processing conditions.
By investing in this comprehensive range of equipment, facilities can not only ensure compliance with industry standards but also enhance the overall efficiency and effectiveness of their recycling processes, contributing to a sustainable future.
Training and Educating Employees
Training and educating employees on quality control processes and the significance of their roles in recycled plastic production is essential to ensure that all team members are actively involved in upholding quality standards. This engagement greatly contributes to the overall success of the operation.
By investing in comprehensive training programs, organizations not only enhance the skill sets of individual employees but also cultivate a culture of accountability and excellence throughout the workforce. When employees comprehend the importance of their contributions to quality control, they are more likely to take ownership of their responsibilities and engage proactively in the process.
Established training modules can encompass essential topics, including:
- Quality assurance techniques
- Best practices in production
- Problem-solving skills to assess quality issues
This level of engagement leads to improved product quality, reduced waste, and increased customer satisfaction, underscoring the critical role of effective employee education in maintaining rigorous quality standards.
Partnering with Certified Recycling Facilities
Partnering with certified recycling facilities significantly enhances quality control efforts by ensuring that recycling processes comply with regulatory standards and industry benchmarks, thereby increasing the reliability of the recycled materials produced.
Incorporating certified partners into recycling initiatives fosters trust and promotes sustainable practices, which are essential in today's environmentally conscious landscape. These facilities undergo rigorous vetting to ensure that they employ advanced methods and technologies for responsible material processing. Collaborating with verified facilities allows businesses to mitigate risks associated with regulatory non-compliance, thereby protecting their reputation.
This partnership contributes to:
- Consistent product quality through standardized processing techniques.
- Enhanced operational efficiency by leveraging the expertise of certified professionals.
- A stronger market position due to a demonstrated commitment to sustainability.
Ultimately, establishing relationships with certified recycling facilities enables organizations to achieve their recycling objectives while adhering to critical compliance regulations.
Conclusion
The efficient management of quality control in the production of recycled plastics and rPE pellets is essential for ensuring compliance with regulations and meeting customer expectations. It also plays a critical role in achieving
sustainability goals within the industry, as demonstrated by leaders such as Poly Source, who are dedicated to enhancing the recycling value chain.
Quality control guarantees that recycled materials, including recycled plastics, can be reliably utilized in manufacturing, thereby fostering trust among consumers and businesses. This increased trust promotes innovation, as companies are more inclined to invest in new technologies that improve the quality of recycled plastics.
Implementing robust quality control measures yields several benefits, including:
- Reduced environmental impact through minimized waste and enhanced packaging materials
- Increased efficiency in recycling processes and equipment investment
- Enhanced product lifespan, thereby driving circular economy initiatives
Ultimately, the commitment to quality in recycled plastics not only supports the success of individual businesses but also makes a significant contribution to global sustainability efforts, resulting in a more resilient and environmentally responsible industry.